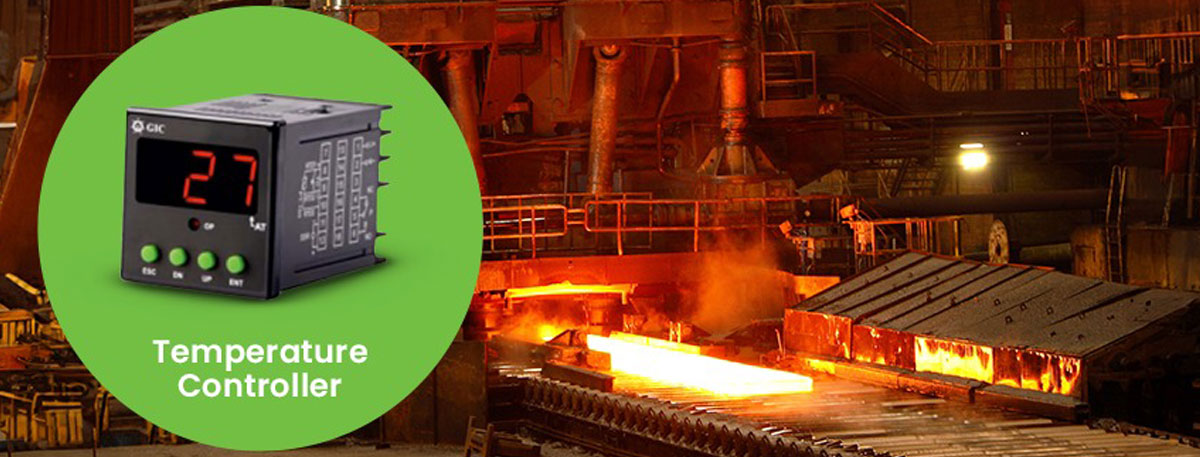
Understanding the Basics of Temperature Controllers
Temperature controllers play a vital role in countless industries, from ensuring consistent product quality in manufacturing to maintaining optimal conditions in scientific research. A temperature controller lies at the heart of this precision, a tool that makes it possible to manage temperatures precisely. GIC General Industrial Controls (GIC) provides robust solutions and expertise in temperature controllers, which we’ll explore in this blog.
Understanding Temperature Controllers
Temperature controllers are electronic devices designed to regulate temperatures with high precision. They receive input from temperature sensors, compare it to a setpoint, and adjust outputs accordingly to maintain the desired temperature. It provides more flexibility, accuracy, and programmability compared to their analog counterparts.
The Role of PID Controllers
PID control is a widely used feedback control technique in temperature controllers. It operates based on three parameters: proportional, integral, and derivative terms.
1. Proportional (P):This term produces an output that is proportional to the current error, i.e., the difference between the desired setpoint and the actual temperature.
2. Integral (I): The integral term considers past errors and integrates them over time to produce a corrective action that eliminates the residual error.
3. Derivative (D): Based on the comparison results, the controller activates heating or cooling elements to adjust the temperature.
Components of a Temperature Controller
Input Sensor:
- The temperature controller starts with an input sensor, such as a thermocouple, RTD (Resistance Temperature Detector), or thermistor.
- This sensor measures the temperature of the system or environment.
1. Microcontroller or Processor:
The heart of the temperature controller is its microcontroller, or processor unit.
This component processes temperature data from the sensor, compares it to the setpoint, and calculates necessary adjustments to maintain temperature within the specified range.
2. PID Algorithm:
A crucial component of many temperature controllers is the PID algorithm.
The PID (Proportional-Integral-Derivative) algorithm calculates control outputs based on proportional, integral, and derivative terms, ensuring precise and stable temperature control by adjusting the control parameters in real time.
3. Output Control:
The output control component converts the adjustments calculated by the PID algorithm into actions that affect the system’s temperature.
That could involve controlling heating elements, cooling systems, or other devices to regulate temperature effectively.
Output control mechanisms can utilize relays, solid-state relays (SSRs), analog outputs, or communication protocols based on specific application requirements.
Sensor Type: Choose a sensor compatible with your application and material properties.
Control Algorithm: PID enables precise control, but on/off control suffices for basic applications.
Output Power Rating: Select a controller with sufficient output power to drive your heating/cooling elements.
Additional Features: Consider features like alarms, data logging, and communication capabilities if needed.
GIC: Your Trusted Partner for Temperature Control Solutions
GIC General Industrial Controls offers a wide range of temperature controllers, sensors, and accessories to meet your specific needs. Our experienced team can assist you in selecting the right products and configuring them for optimal performance. We also provide technical support and training to ensure you get the most out of your temperature control system.